A 2 DoF origami spring robot actuated by two servos, equipped with directional friction pads
Overall:
This project started as a Cal Poly SURP in 2023. I joined in the beginning of 2024. I worked under Dr. Mohammed Hasan with undergraduate students Micheal Freeman, Conor Schott, Carter Josef, and Col Cook.
Most of my work was on getting the robot to move well. The origami pattern was already created and worked well. We needed to program it for cyclic motion and keyboard inputs. I worked to characterize the stiffness of different origami springs and generalize it to certain metrics of the springs.
There were many developments in the material of the origami, the design of the friction pads, the material of the string, and the method of control.
We published a paper at the 2024 ASME IDETC-CIE where Michael and Conor presented our work.
The paper can be found on the ASME Website.
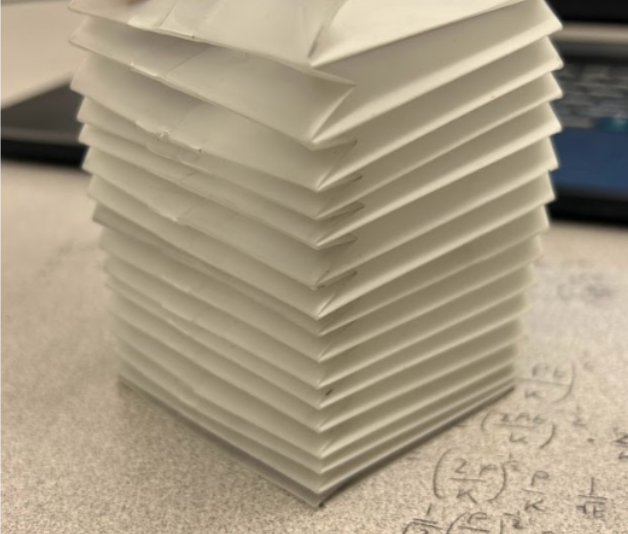
The Rigiccordion origami pattern is rigidly foldable which means the Rigiccordion maintains structural stability under large deformations. This allows the robot to compress completely without the original perimeter shape changing. The Rigiccordian is far less complex to fold compared to some other rigidly foldable options. Its stiffness is linear until near complete compression.
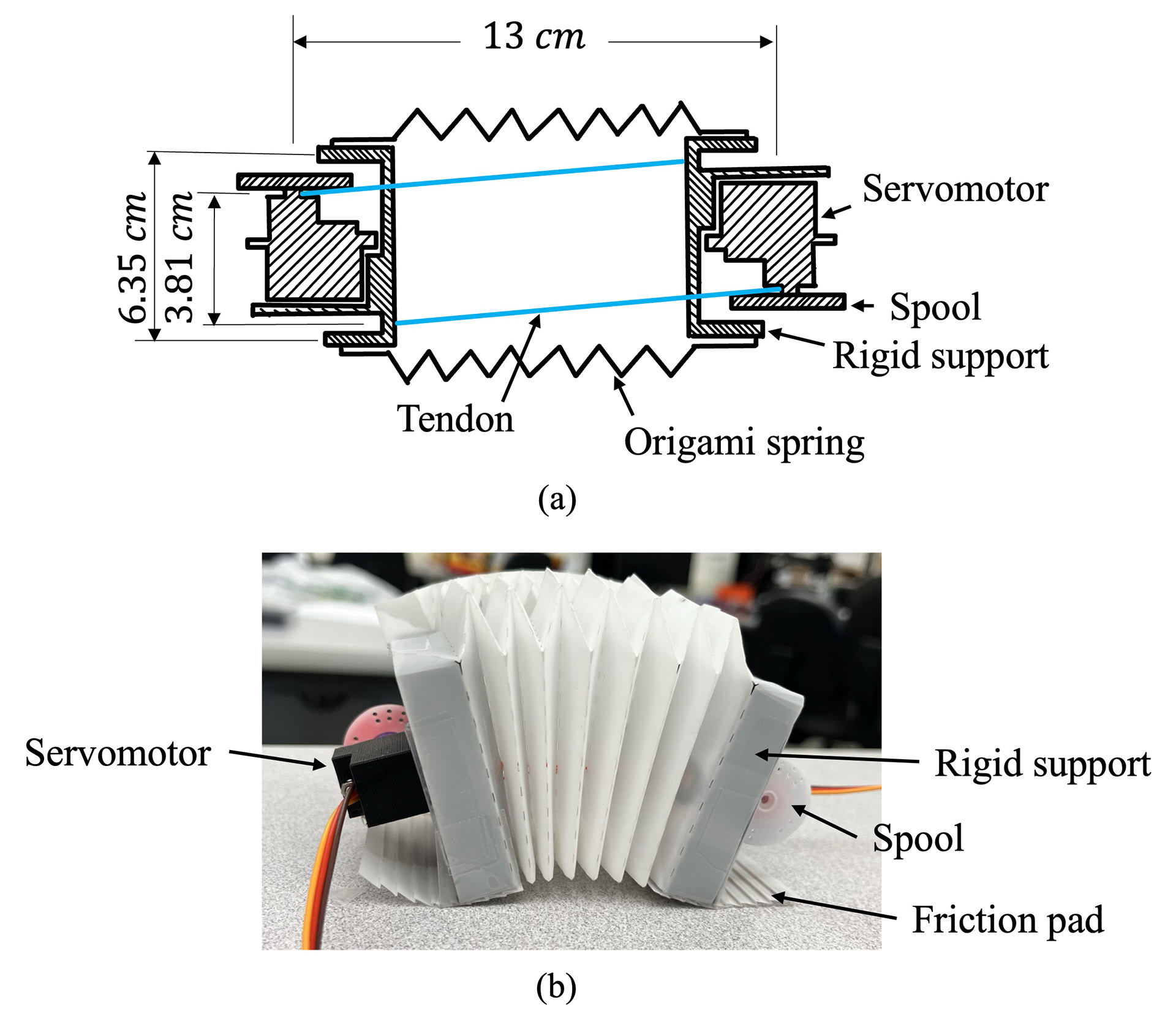
The robot consists of two servo motors that sit on opposite sides of the robot. They have a tendon that connects directly to the other side that is off-center. This allows the robot to compress and decompress in unique ways which can illicit forward motion and turning motion. The friction pad on the bottom of each support makes the forward motion possible.
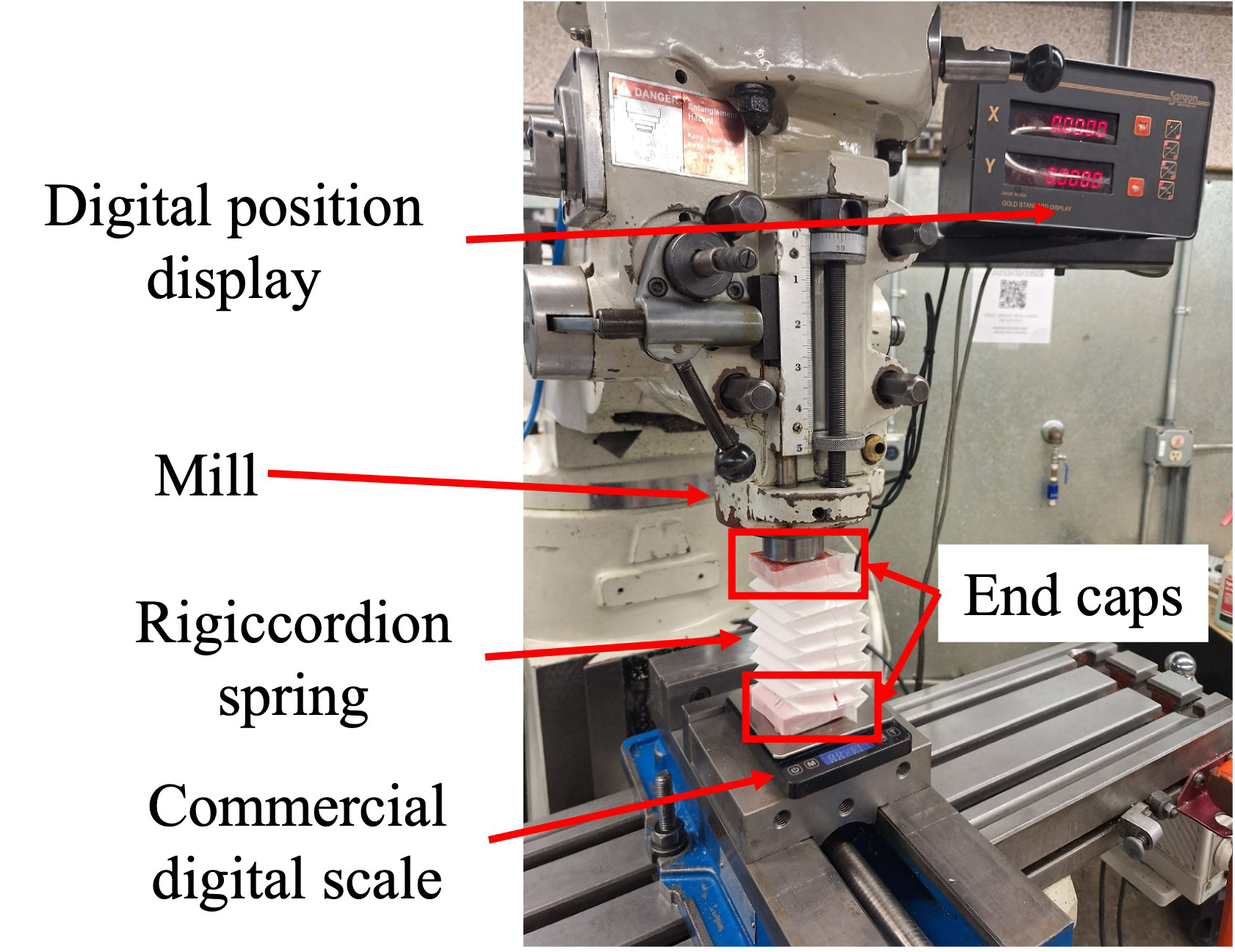
To characterize and generalize the stiffness of the Rigiccordion spring, we completed stiffness tests using a mill and commercial scale. This allowed us to show the linearity of the spring's stiffness. We also developed empirical correlations to try to predict the stiffness of different size Rigiccordions. These correlated relatively well using the perimeter of the spring, the number of folds, and the radius of each fold along with a material factor.
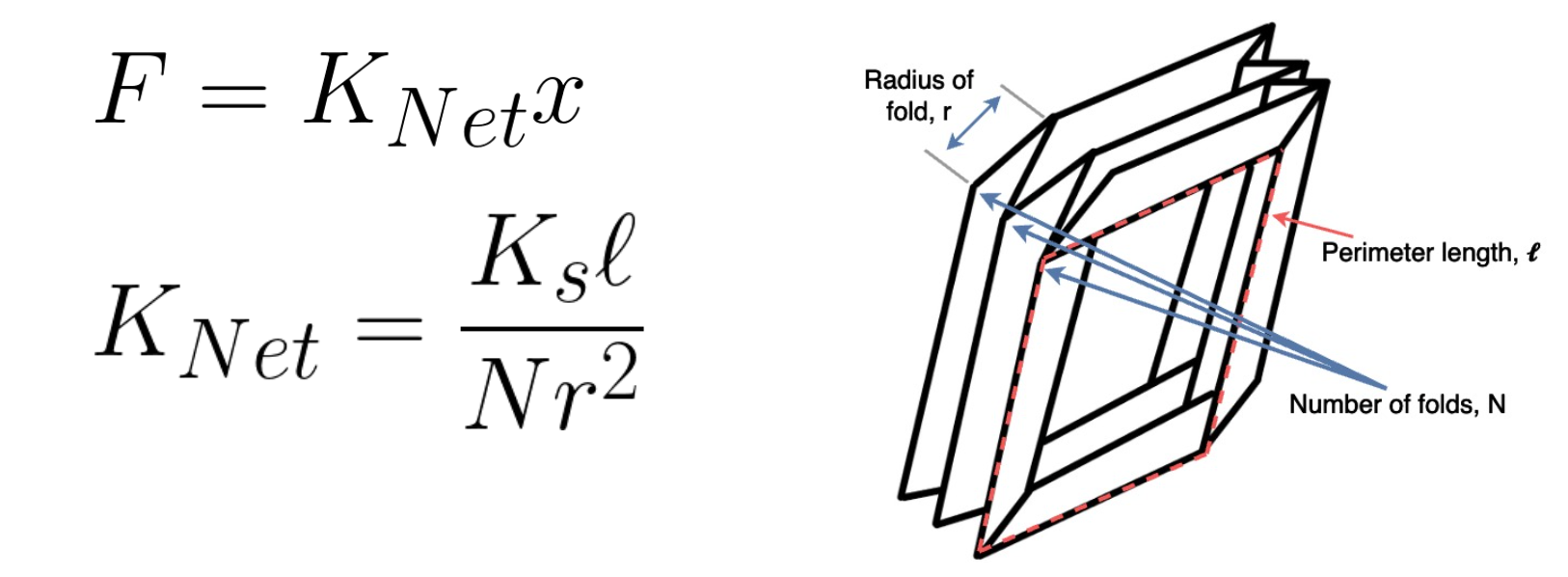
Stiffness modeling equations their definitions
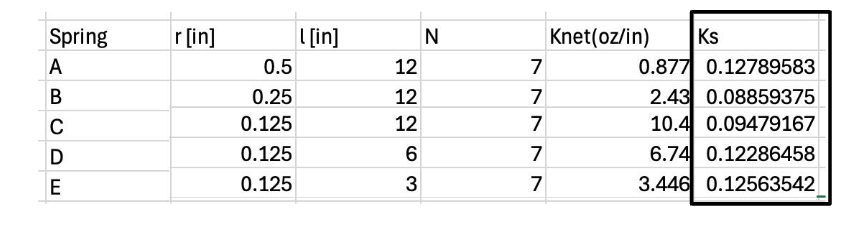
Ks is the material stiffness coefficient. For Inkjet paper, Ks was 0.112 oz-in with a standard deviation of 0.0167 oz-in.
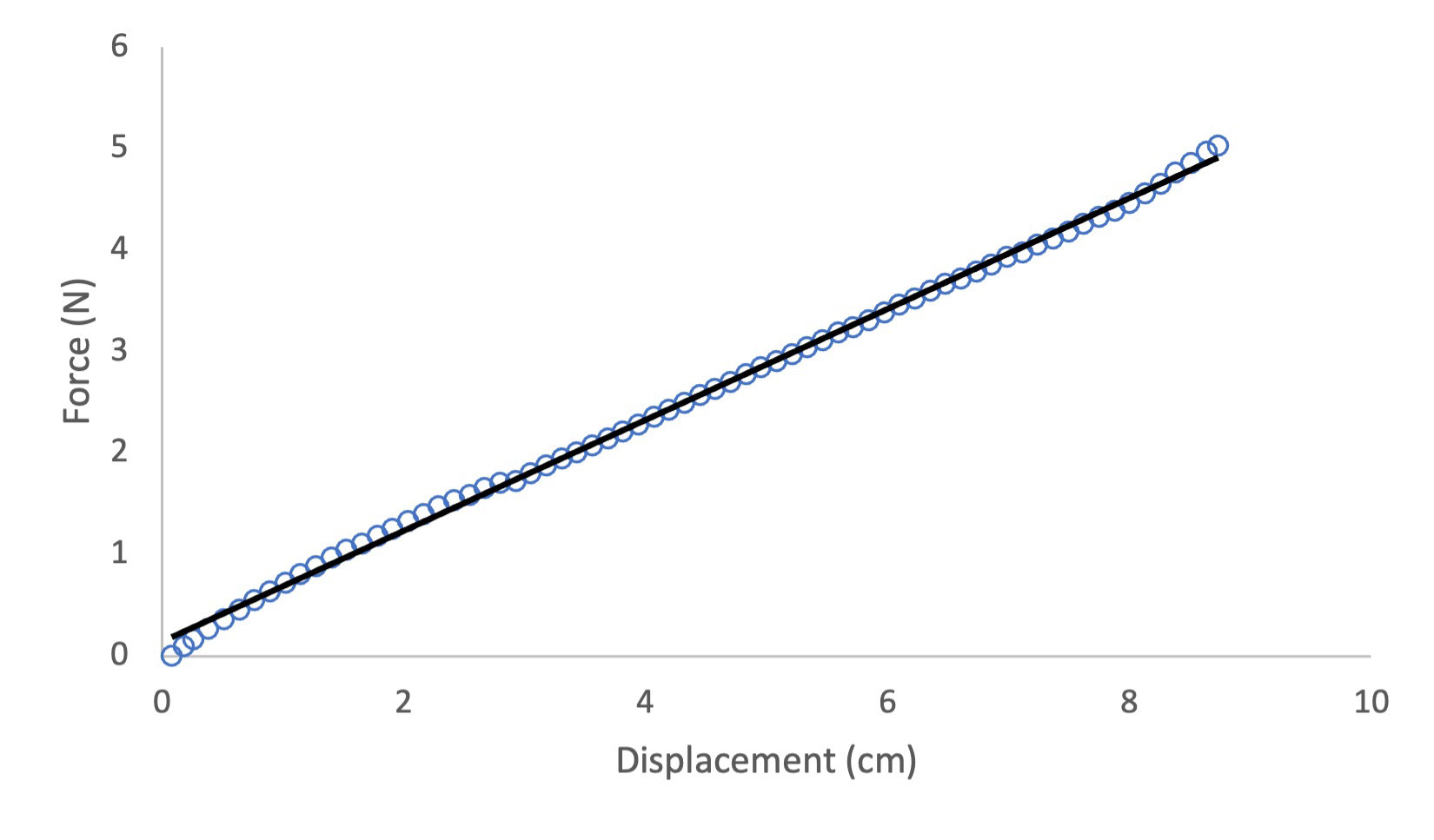
Stiffness curve for a Rigiccordion made of Mylar
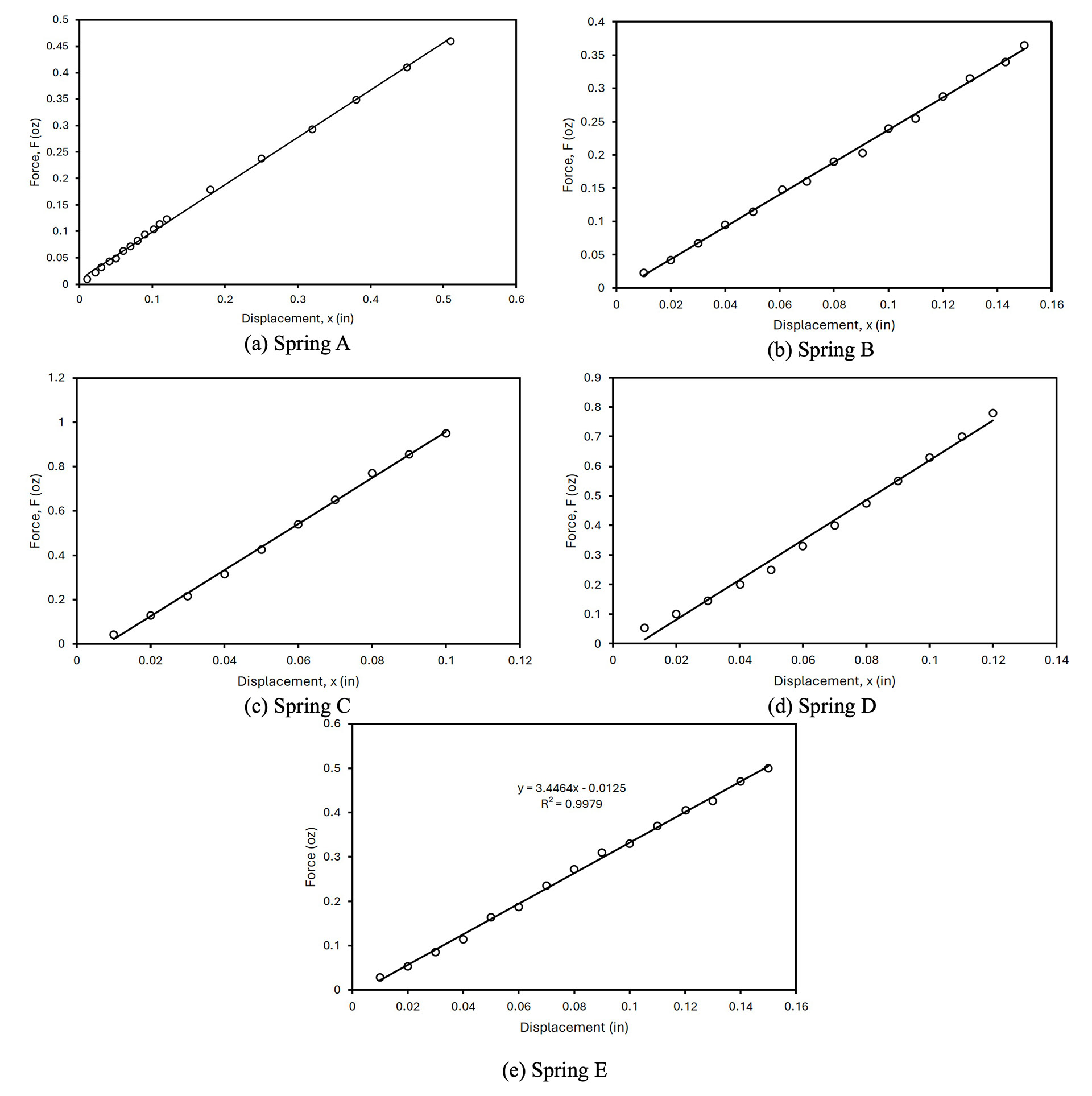
Stiffness curves for Inkjet paper Rigiccordion springs